The reasons why double-layer oil tanks are popular in the market and the safety issues in their use
With the continuous development of social economy, oil tanks have become a common tool equipment in daily production, but few people are clear or proficient in the acceptance standard inspection of oil tanks. Today we will introduce to you how to conduct reasonable leak testing in the production process of double-layer oil tanks.
Oil tank leakage detection
Permeation test: The double-layer oil tank welds are inspected by kerosene penetration method. The equipment welds are coated with chalk slurry. After drying, kerosene is brushed inside. After half an hour, it is checked. If there are no kerosene leakage spots, it is qualified.
Air tightness test: The equipment is tested for air tightness, and the pressure rises slowly. After reaching the specified test pressure, the pressure is maintained for 10 minutes, and then reduced to the design pressure. The welds and joints are brushed with soapy water. Check that there is no bubble to be qualified.
If the double-layer oil tank drain valve fails, the mechanic should immediately install the blind plate and report the situation to the superior in time. Fire and explosion: When such an accident occurs, the relevant operators should immediately stop the water discharge operation and close the oil tank gate valve; quickly send a fire alarm signal and implement fire fighting.
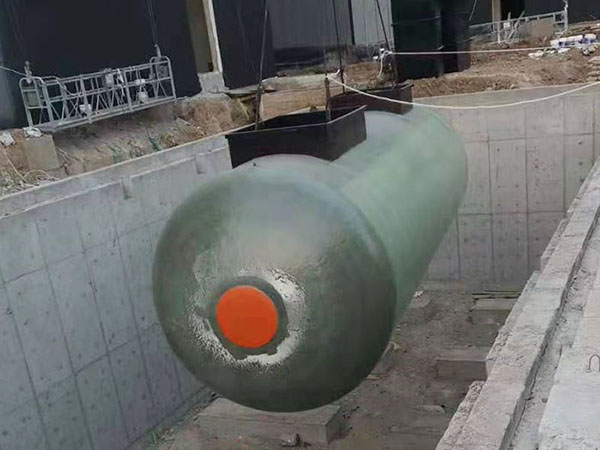
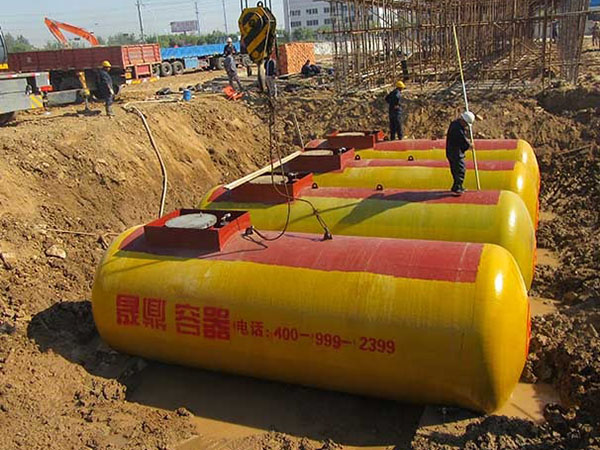
The benefits of regular cleaning of oil tanks
In the oil tank market, the service life of many oil tanks is inconsistent with the markings on their instructions, and some are far from it. In fact, these are all caused by the failure to maintain the oil tanks on time and in quantity during the use of the oil tanks.
Shengding oil tanks generally have a long service life. Long-term storage of oil often ignores the regular inspection and cleaning of Hainan oil tanks. Shengding oil tanks will corrode and leak due to long-term use. If the inspection of Hainan oil tanks is neglected, it will cause great safety hazards.
The health of Shengding oil tanks also threatens the surrounding environment and the safety of Hainan oil tank areas. It is crucial to keep Shengding oil tanks safe and clean and scientifically control the corrosion of Shengding oil tank walls. Applying an anti-rust layer on the inner wall of Shengding oil tanks can better avoid the catalytic effect of metal on oil oxidation.
The slag at the bottom of the gasoline storage tank is mainly rust. When the Shengding oil tank is unloading oil, the sediment at the bottom of the tank will be floated up, and the powdery rust will dissolve into the oil. If the car is added with such oil, it will cause great harm to the vehicle itself. The sediment at the bottom of the diesel tank accumulates for ten years, and the sludge at the bottom of the tank will reach about 15 cm.
Regular cleaning of the tank and the anti-corrosion coating on the inner wall is an effective measure to solve the metal oxidation and rust and slow down the deterioration of the oil; the longer the Shengding oil tank is stored, the more sediments will be produced by oxidation, and the more serious the impact on the quality of the oil.
Once the metal of the Shengding oil tank is corroded and perforated, a large amount of oil will leak, causing economic waste and environmental damage, and even causing the risk of fire. Therefore, the bottom of the tank must be checked once a year to determine whether it needs to be cleaned.
The absolute advantage of double-layer oil tanks
If the outer tank leaks, the gas or test liquid with a certain pressure in the double-layer gap will enter the soil. Similarly, the pressure or liquid level in the double-layer gap will change, triggering the sound and light alarm. At this time, since the inner tank is intact, the storage liquid is safe; only gas or test liquid enters the soil, so the soil and groundwater are also safe.
Let's analyze it first. SF stands for steel reinforced glass fiber double-layer oil tank. It is a double-layer oil tank with a glass fiber reinforced plastic (i.e. glass fiber reinforced plastic) anti-seepage jacket added to the single-layer steel oil tank. Because the storage liquid in contact with the inner tank and the soil and groundwater in contact with the outer tank belong to different media, the corrosion rate of the tank material is different, and the probability of leakage at the same time is almost zero. Therefore, it can prevent the storage liquid from leaking out of the tank, achieving production safety and environmental protection.
Structure:
1. Inner layer: Made of 6mm thick Q235-B steel plate, the strength is improved compared with the ordinary single-layer oil tank with a thickness of only 5mm.
2. Outer layer: reinforced glass fiber, with a thickness of more than 2.5mm, good pressure resistance and shock resistance. It has corrosion resistance and electrical corrosion resistance;
3. Through gap: 0.1~3.5mm; 300° range, no firm support.
4. Strengthened structure: Inner tank reinforcement
5. Detection equipment: Leak detector monitors in real time 24 hours a day, and issues an alarm when the liquid level at the bottom of the gap space is detected.
If the inner tank of a double-layer oil tank leaks, the gas or detection liquid with a certain pressure in the double-layer gap will enter the inner tank at normal pressure; the pressure or liquid level in the double-layer gap will change, triggering the sound and light alarm. After the storage liquid leaks into the double-layer gap, the storage liquid will not leak out because the outer tank is intact. Therefore, the storage liquid, soil and groundwater are all safe.
Leak detector
There is a through gap space between the steel inner tank and the FRP outer tank, which mainly has three technical characteristics: safety,
environmental protection, and economic practicality. It can be seen from time to time that the double-layer oil tank is the most effective among other oil tanks!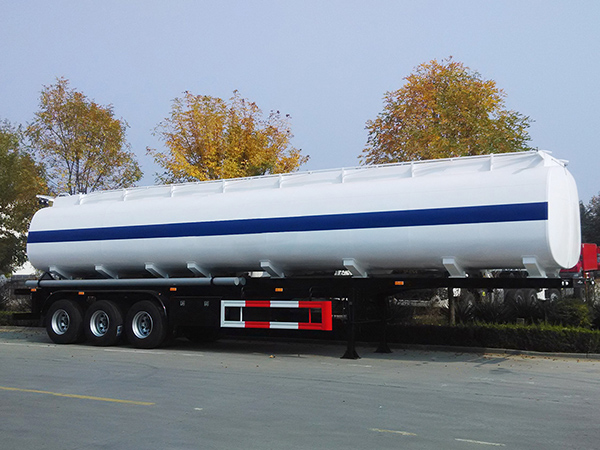
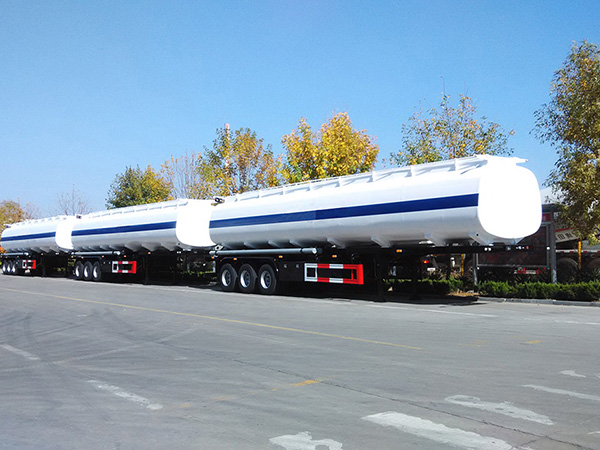
Safety matters for cleaning oil storage tanks
1. Carry out cleaning operations in severe weather such as high temperature, rain, strong wind, and thunder and lightning.
2. Ventilate inward under conditions of low air pressure and unfavorable oil and gas diffusion.
3. Use non-explosion-proof ventilation ducts.
4. Failure to detect the oil and gas content around the tank mouth and in the tank.
5. Construction is carried out without a safety officer on site.
6. Failure to ventilate the tank.
7. Workers enter the tank even when the oil and gas content in the tank exceeds the standard.
8. Construction workers enter the tank without a safety rope.
9. Improper use of protective equipment or failure to function.
10. Breathing pipes are entangled or compressed, preventing air from entering.
11. Use non-explosion-proof lighting fixtures.
12. Lighting fixtures fall or light sources are damaged to produce sparks.
13. Use non-explosion-proof tools, or tools without electrostatic equipment.
14. Construction workers do not rotate and work in the tank for a long time.
Written by
TAIAN SHENGDING METAL CONTAINER MANUFACTURING CO., LTD.
Editor Wang
www.self-bunded-tank.com
WhatsApp : +86 152 5486 3111
Email :shengdingtank@126.com
- WhatsApp
- E-MailE-Mail:shengdingtank@126.com
- WeChatWeChat:15254863111