Nine major safety inspections make it impossible for skid-mounted gas stations to hide safety hazards
During the operation of skid-mounted gas stations, safety inspections are the most routine and most complex inspection items. A little carelessness will cause immeasurable consequences. Today we will mainly explain to you the nine most important items for safety inspections of skid-mounted gas stations. In fact, here we mainly talk about the safety inspection of double-layer oil tanks in skid-mounted gas stations, because the safety index of double-layer oil tanks is basically the safety index of the entire skid-mounted gas station. Let's take a closer look.
(1) Add dye to the water and perform a water pressure test to detect leaks. In addition, you can listen to the sound on the tank wall or install an acoustic sensor on the tank wall, set up an observation well in the tank area for monitoring, and use a dipstick to detect the tank liquid level and leaks.
(2) Kerosene tightness inspection weld: Kerosene has extremely strong penetration. Apply kerosene to the weld on the tank wall for tightness inspection. Remove dirt, apply white powder emulsion, and spray kerosene on the weld on the other side after drying. If there are no spots on the surface of the white weld after 12 hours of kerosene spraying (the time can be extended when the temperature is low), the weld meets the requirements.
(3) When the double-layer tank is receiving and sending operations, leak detection is performed based on the difference in actual inflow and outflow.
(4) Double-layer tank wall test: Perform a water filling test on the newly built or repaired oil tank to detect whether the double-layer tank wall is tight, and perform an appearance inspection of the oil tank wall plate and weld.
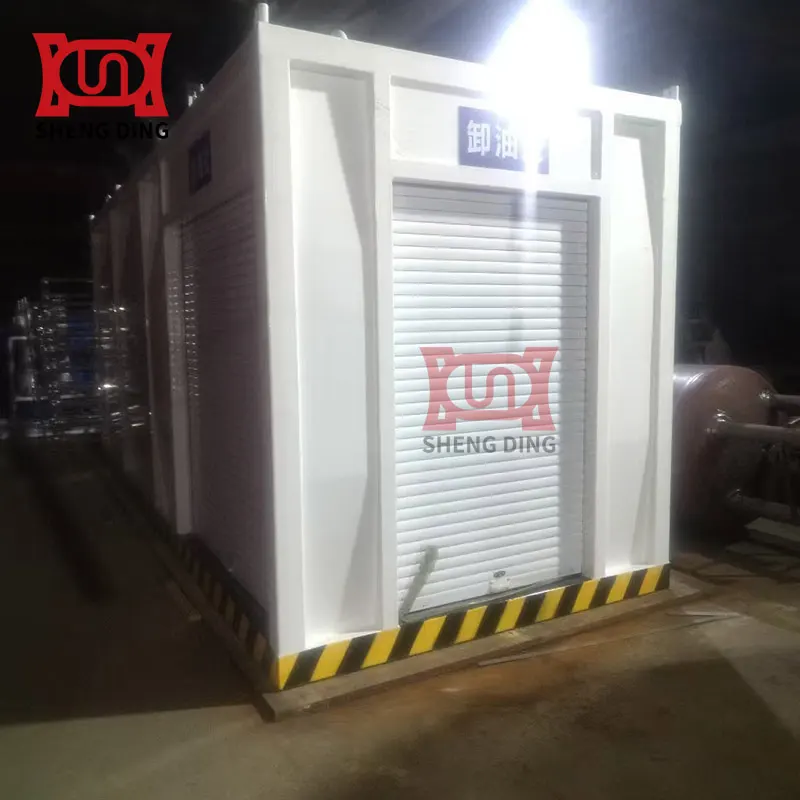
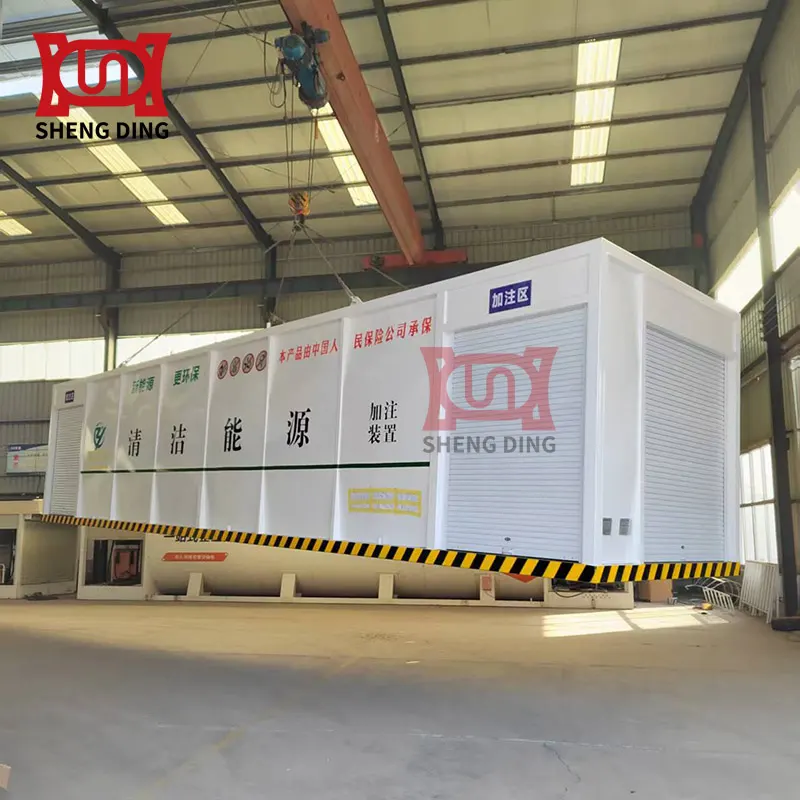
(5) Double-layer tank bottom plate weld inspection: When the vacuum leak test method is used to test the tightness of the bottom plate, apply soapy water to the weld and cover the vacuum box for observation.
(6) Leak detection is achieved by detecting the change in the volume of the oil product in the double-layer tank. This method is not easy to detect small leaks.
(7) Measure the bottom pressure of the double-layer tank and calculate the weight of the medium in the tank to detect oil tank leakage. If the mass continues to decrease, it means that a leak has occurred.
(8) Double-layer tank wall thickness inspection: Materials must be inspected and put into storage before entering the site. Ground double-layer tanks are mainly inspected by ultrasonic waves, which is highly efficient.
(9) Tank bottom inspection: Magnetic flux leakage scanning technology detects the corrosion condition of the bottom plate of the oil tank (such as corrosion depth and area, crack length, etc.). The detection principle of this instrument is: the magnetic flux leakage scanner detects the bottom of the oil tank. When the bottom plate of the oil tank has defects, the magnetic field distribution will change, and the sensor can detect it. The disadvantage is that some areas will be missed and the bottom of the tank cannot be fully inspected. During the inspection, the bottom of the oil tank is free of debris and dry. In addition, helium can be injected into the bottom plate of the oil tank to detect the leakage point of the tank bottom.
The above nine items are the daily safety inspection items of double-layer oil tanks in skid-mounted gas stations. These items are very important. Each item is closely related to life and property. Therefore, safety inspection items are the most important regardless of whether they are simple or cumbersome.
Written by
TAIAN SHENGDING METAL CONTAINER MANUFACTURING CO., LTD.
Editor Wang
www.self-bunded-tank.com
WhatsApp : +86 152 5486 3111
Email :shengdingtank@126.com
- WhatsApp
- E-MailE-Mail:shengdingtank@126.com
- WeChatWeChat:15254863111